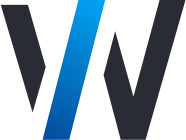

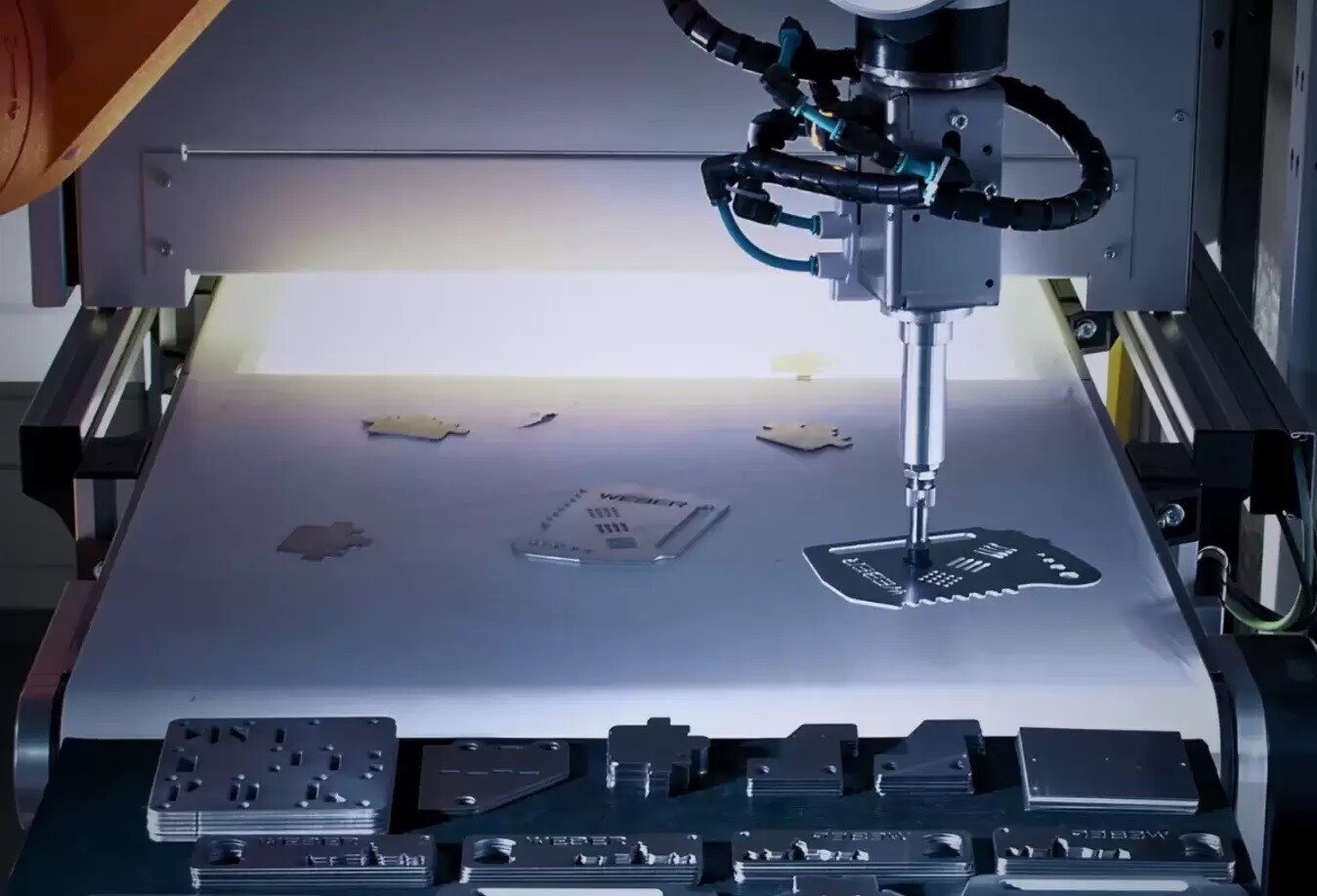
Optimally automated - for efficient production processes.
Increase the efficiency of your machine by implementing an automated loading system in your unloading system. The degree of automation can be further increased through the integration of automated infeed and outfeed solutions, right up to completely unmanned production.
Automation solution for loading conveyor belts
Our innovative systems rely on an integrated camera system for the intelligent detection of all workpiece stacks on the pallet. The precise calculation of the number of workpieces from the stack height enables efficient uniform distribution, which in turn ensures even tool wear during further processing by a sanding machine. This approach not only guarantees maximum efficiency, but also optimizes your production control to a new level.
WEBER series
HS-4-1000
Workpiece size | 20 x 20 mm to 750 x 750 mm |
Workpiece geometry | Flat workpieces, any free form |
Workpiece material | Metal, wood, plastic |
Load capacity | max. 8,4 kg |
Working width | max. 1350 mm |
Cycle time | approx. 25 parts/min. |
Max. stacking area | 1200 x 800 x 370 mm |
Robot type | Stäubli TS2-100 |
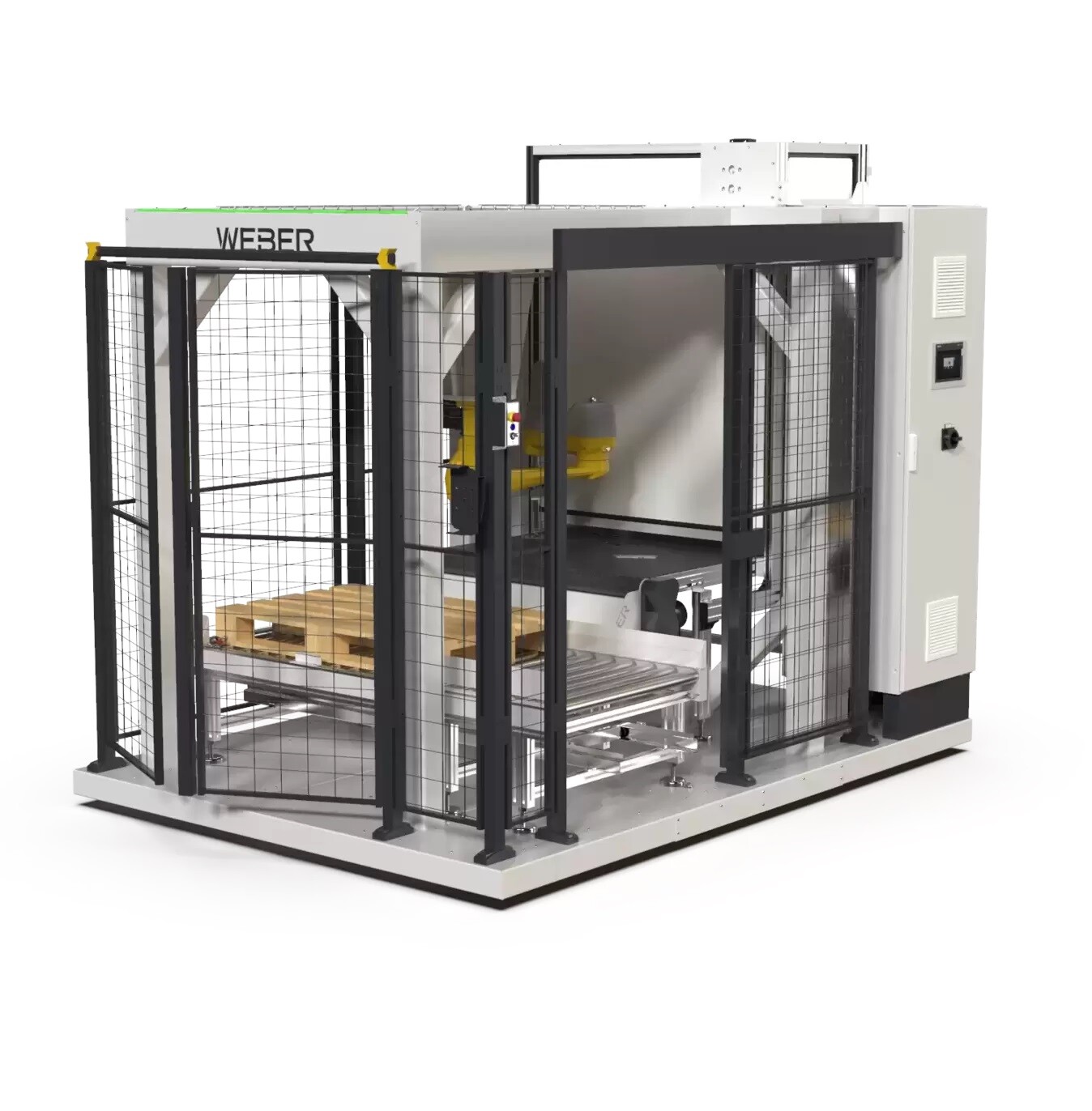
Bin picking: Efficient solutions for the automated loading of chaotically arranged workpieces
Conventional loading situations require the industrial robot to pick workpieces from a flat conveyor belt. However, some production processes require loading from unsorted load carriers, which often means manual intervention and additional manpower. Bin picking from WEBER automation solves this problem, enabling the automated loading of chaotically arranged parts without the need for separation systems.
The Bin Picking system masters the challenges of ever smaller batch sizes and optimizes cycle times in the millisecond range. A single application recognizes and separates different products. With Bin Picking, the robot literally reaches into the box, recognizes disordered workpieces in load carriers, picks them up and places them separately. The position and geometry of the workpieces is irrelevant; even mixed load carriers are unloaded automatically. Bin picking offers greater flexibility and space savings compared to separation systems and opens up new automation options compared to conventional applications.
Fact check
+ 3D vision system: projector and 4 cameras for stable workpiece detection
+ Automatic robot path calculation using path planning algorithm
+ Removal from load carriers up to 1280 x 1280 mm, including intermediate layers
+ With integrated interference contour detection and intelligent robot path planning, ideal for containers that are difficult to access
+ Reduce personnel costs and minimize unhealthy work
+ Reduce cycle times and increase productivity
+ Maximum adaptability, even for complex production processes
Feeder systems for loading a conveyor belt
Our feeder systems offer flexible parts feeding in large quantities. The integration of image processing, robotics and special software provides customers with customized solutions. The systems enable smooth batch changes and can be expanded to include additional components such as container tilting devices and dosing bunkers. This creates a holistic solution for efficient production. One specific example is loading via a vibratory bowl feeder, which enables the correct positional sorting of bulk material and industrial bulk parts. An electromagnetically driven upper sorting section aligns workpieces on a circular spiral using the micro-throw principle and feeds them in a defined position to a downstream accumulation section. This integrated solution not only maximizes efficiency, but also optimizes the overall performance of the production processes.
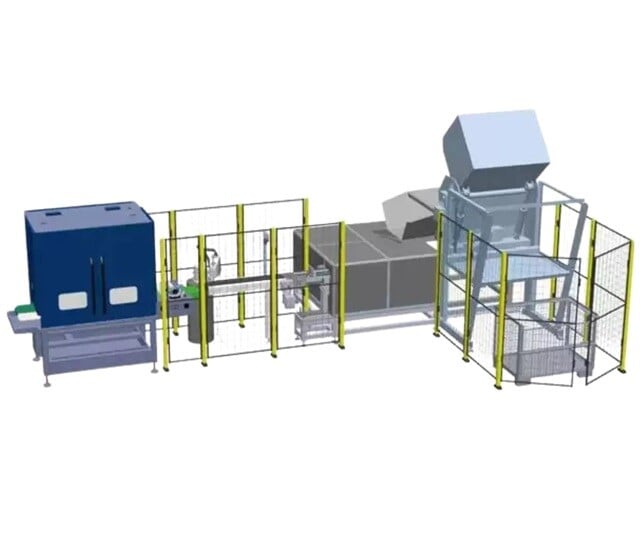